If you are looking for a high-purity solution for your pharma process needs, you have just landed on the right blog!
In this post, we will discuss exactly what orbital welding is and the advantages of using an Orbitally Welded System. Without further ado, let’s dive directly into the discussion:
Table of content
- What is Orbital Welding?
- What are the Advantages of Using Orbitally Welded Systems?
- TSA’s Orbitally Welded WFI
- Conclusion
- FAQs
What is Orbital Welding?
As the name suggests, Orbital welding is a special welding technique in which the welding electrode or torch is rotated mechanically around a fixed object, typically a pipe or a tube. It uses Tungsten Inert Gas (TIG) or Gas Tungsten Arc Welding (GTAW) methods, which have excellent control and produce clean, high-purity welds.
Orbital Welding is useful where manual welding is challenging, such as in tight spaces and thin-walled tubes. The process of Orbital Welding ensures welds are high-quality with minimum defects, thereby making it ideal for pharma where sterility is critical.
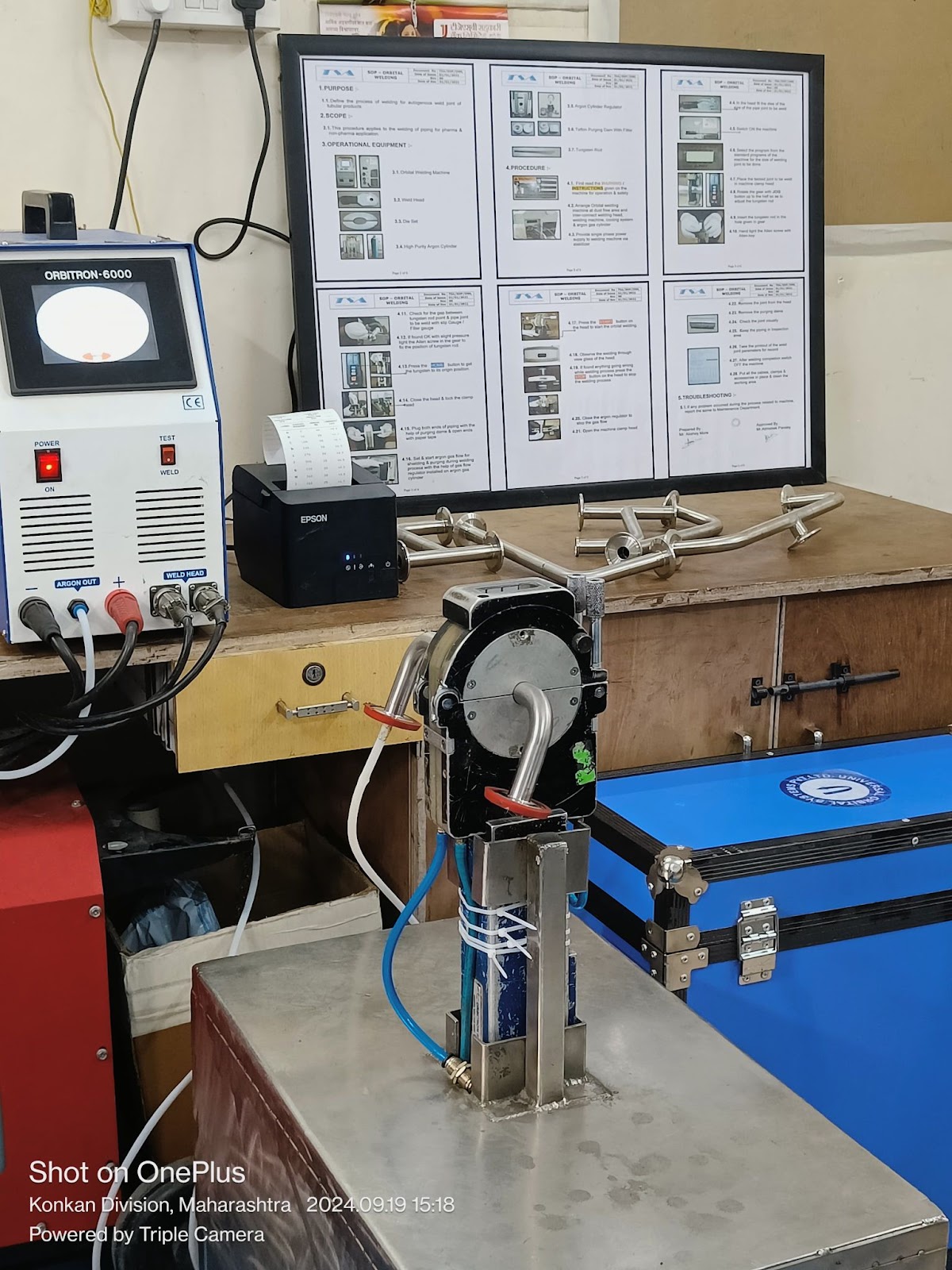
What are the advantages of Using Orbitally Welded Systems?
Orbital welding is preferred over other types of welding, such as Manual Tungsten Inert Gas (TIG) welding, Metal Inert Gas Welding (MIG), and Plasma Arc Welding (PAW), in the Pharma Industry for the following reasons:
1. High Purity and Hygiene
Orbitally Welded systems ensure sterility well maintained for product formulation, cleaning, and injection. For example, the piping systems carrying WFI must be free from particulates, microbes and other contaminants. Since Orbital welding results in clean welds, it reduces the risk of contamination. Thus ensuring the purity by eliminating crevices, cracks or inclusions where microbes could thrive.
2. Consistent and Automated Welding
Since the orbital welding process is fully automated and can be controlled by pre-set parameters, you can eliminate human error by up to 100%. Process automation ensures consistency in pharmaceutical production, a much-desired quality to thrive successfully in the market in the long run.
3. Eliminates the Need for Filler Material
Usually, the orbital welding process makes use of the Tungsten Inert Gas (TIG) Method without any filler material. This helps maintain the integrity of the stainless steel or any other high-purity materials used to construct WFI systems.
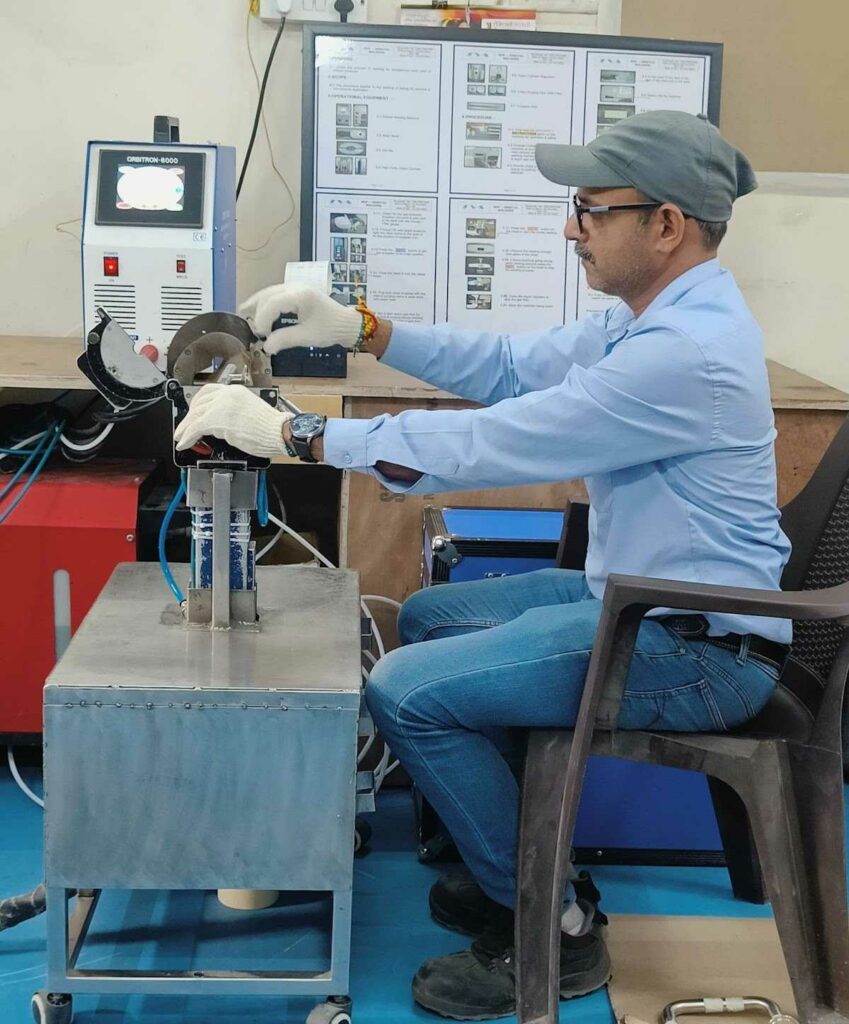
4. Compliance with Regulatory Standards
Every system, process, and material used in the pharma industry is obliged to comply with the regulatory standards set by regulatory authorities like FDA, GMP, and ASME BPE, which mandate hygienic design and cleanability. By using Orbitally Welded systems, the worry of compliance is off the list as it allows detailed documentation and traceability, assisting in the validation process.
5. Reduced Downtime delays
Owing to the precision and the repeatability of the orbital welding process, the downtime delays are minimized as there is a low need for rework or repair. As the welds are smooth, clean, and easy to inspect and validate, the time required for conducting routine inspections is minimal, thereby increasing productivity.
6. Safety and Durability
By choosing an orbitally welded water purification system, you can be assured of minimal risk of leaks or failures, a critical factor in decision-making when operated at high temperature and pressure.
Since orbital welding produces smooth welds, avoiding any crevices, you also reduce the chances of corrosion damage to the system. As the equipment will be exposed to a variety of chemicals and solutions, it is of utmost importance to invest in the corrosion-proof system.
TSA’s Orbitally Welded WFI
At TSA, we ensure you receive process equipment and solutions of premium quality. The water produced by our WFI surpasses the most stringent standards globally.
As we understand the significance of contamination-free systems in the pharma industry, we manufacture state-of-the-art technology to suit your advanced sterile processes. Our Multi-column Distillation Plant is a uniquely efficient purification system with flow rates ranging from 80 LPH to 5000 LPH. It has a sleek mechanical construction in SS 316L with electropolished contact parts. The joints are orbitally welded with a video borescope to ensure compliance with USFDA 21 CFR part 11 and GAMP 5.
Choose our pre-passivated system that offers high flexibility with a variable production capacity of up to 80% without additional plant modification.
Conclusion
We understand that balancing your budget may be challenging while considering investing in an orbitally welded WFI system. TSA has been a trustworthy partner in the industry for the past 20 years. Delivering our expert advice and solutions around the clock in over 600 countries, we are here to serve more!
Do not worry, as we are here to support you. Contact us at TSA, and we can craft a budget-friendly solution with zero compromise on quality for you.
FAQ’s
1. How much does an orbitally welded WFI system cost?The cost of an orbitally welded WFI system depends on its size, the materials used, and the complexity of installation. Usually, these systems are costly because of the high-quality material, such as 316L stainless steel, and the requirement for specialized welding equipment and skilled labor.
2. How is orbital welding inspected and validated in WFI systems?Non-destructive methods like X-rays or ultrasonic testing are used to inspect and validate orbital welding in WFI systems. In addition to these complex tests, simple tests like visual inspection can be done to detect cracks or corrosion in the weld.
3. What are the challenges of using orbitally welded WFI systems?In addition to the high initial cost of installing the orbitally welded system, the routine maintenance and inspection could be challenging as it may result in operational downtime and could disrupt the production schedule.
4. How does orbital welding reduce contamination in WFI systems?By Orbitally Welding the pipes to the system, one can ensure minimum contamination as the welds are smooth, eliminating any crevices, cracks or inclusions where particulates could accumulate or microbes could grow. The precision of the automated welding process ensures the joints are consistent, ensuring the product quality is consistent and contamination-free.
5) What materials are used for piping in WFI systems?Most commonly, high-purity stainless steel, precisely 316L Stainless steel material, is chosen because of its high durability and resistance to corrosion due to chemicals. Also, this material is highly compatible with extreme conditions during the sterilization processes, such as high temperature and pressure.