Just like government policies keep changing, technology evolves, too, and to remain relevant in the market, it is essential to stay updated. We are here with another blog to update you on the advancements in the Bio Kill Tank System. Without further ado, here are the top 6 advancements shaping the future of the Bio Kill Tank Systems:
Automated Sterilization Processes
Efficient sterilisation of the Bio Kill tank ensures your product is safe and complies with regulatory standards. It also enhances the operational efficiency and prevents product recalls.
Cleaning systems like CIP (Clean-In-Place) and SIP (Sterilize-In-Place) are intelligent solutions to automate cleaning and sterilising practices without requiring the disassembling of equipment.
You can now integrate steam generation and distribution systems with the Bio Kill tank system to automate sterilisation and temperature and pressure sensors to monitor and control these parameters during sterilisation.
TSA offers PLC and SCADA automation systems to ensure optimal performance and safety.
Energy-Efficient Designs
With increasing awareness of environmental sustainability, the UN has set 17 sustainable development goals for companies to follow. You can design energy-efficient Bio Kill tanks to align with these goals and support your organisation’s growth.
Heat recovery systems, like heat exchangers and thermal storage systems, can be used. Our heat exchangers recover waste heat from hot effluent streams and preheat incoming cold streams, saving the energy required for heating.
Besides heat exchangers, thermal storage systems are applicable to store excess thermal energy for later use, balancing energy demand and supply. You can opt for Low-temperature sterilisation methods, such as UV, ozone, or chemical sterilants, which require less energy than traditional steam sterilisation.
Additionally, optimising the physical layout of tanks and auxiliary systems to reduce energy losses in piping and distribution lowers operational costs and reduces the carbon footprint.
Enhanced Safety Features
Maintaining worker safety holds prime importance. Using leak detection sensors to detect leaks and spills quickly enables prompt action to mitigate hazards.
The gas detection system is now used to detect hazardous gases like ammonia, chlorine, and hydrogen sulfide to prevent exposure risks.
To ensure safe operation, Bio Kill tanks are equipped with pressure relief valves to prevent over-pressurization. Burst discs act as secondary pressure relief measures, designed to rupture at a pre-set pressure to protect the tank.
Double-walled Bio Kill Tanks can provide an additional containment layer in case of primary tank failure. Containment basins and dikes are now available to capture and contain spills or leaks.
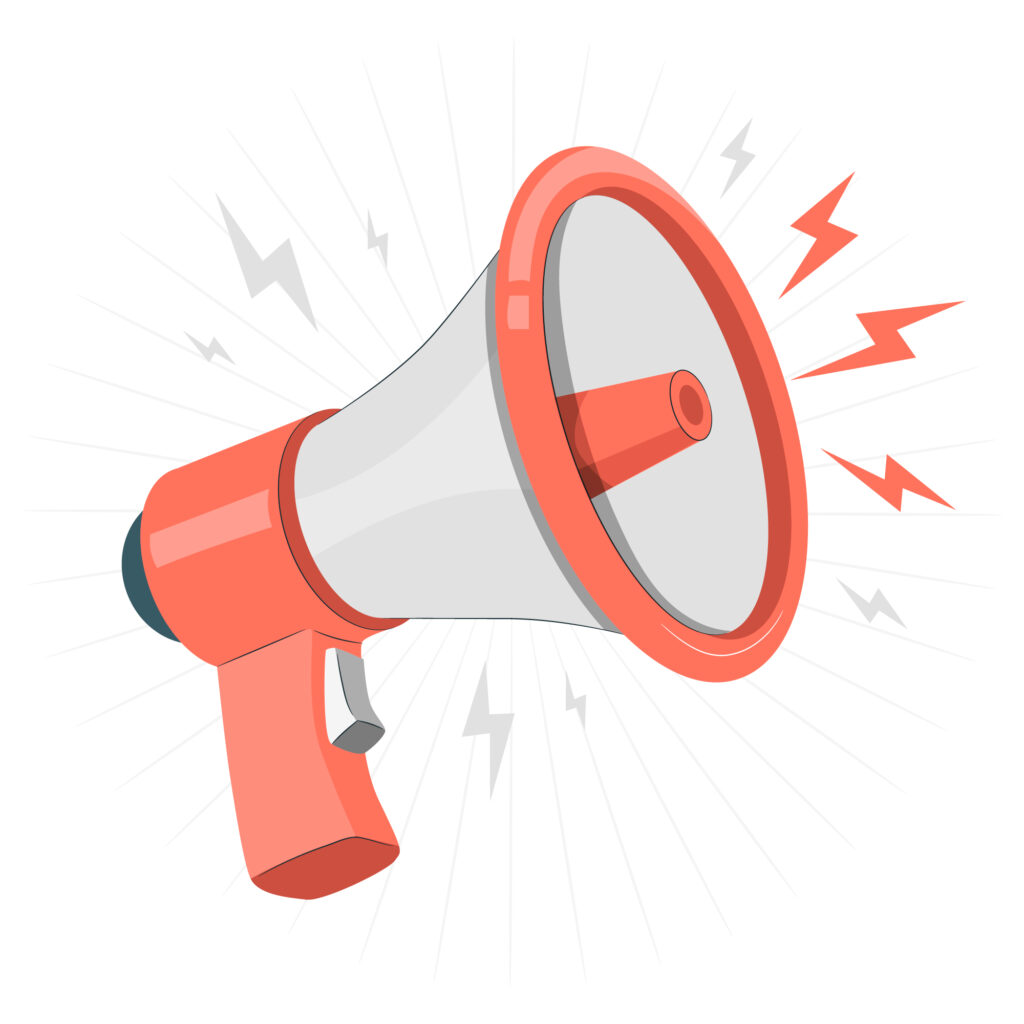
As the saying goes, “Prevention is better than cure.” An emergency response system with integrated alarms and notifications should be set up to alert personnel and emergency responders to hazardous conditions. Install valves that automatically or remotely shut off in an emergency to isolate the tank.
Improved Material Durability
Advances in materials science have led to more durable and longer-lasting Bio Kill tanks.
Besides regular high-grade stainless steel alloys, such as 316L and 904L, manufacturers use titanium and its alloys for their high resistance to corrosion and biofouling. Recently, composite materials like fibreglass-reinforced plastics (FRP) have been used to produce Bio Kill tanks, imparting high strength and corrosion resistance.
The application of epoxy coatings is gaining popularity as they provide a durable and chemically resistant barrier, while polyurethane coatings offer excellent abrasion resistance. Ceramic coatings protect tanks against extreme temperatures and wear.
The electropolishing technique has recently been used to eliminate microscopic imperfections, reducing the risk of corrosion and contamination. By passivating the stainless steel surfaces, you can remove free ions and enhance the formation of a protective oxide layer, thereby improving corrosion resistance.
Advancements in nanotechnology have led to the development of self-healing coatings that can repair minor damage automatically, extending the tank’s lifespan. Hybrid materials like metal-polymer hybrids have been used these days to manufacture bio-kill tanks as they offer the best of both worlds: strength, flexibility, and corrosion resistance.
Scalability and Customization
Systems must be tailored to specific needs and should be scalable as required. Components like pumps, valves, and sensors can now easily be swapped or upgraded.
Standardised, interchangeable parts are now available and can be used across different tank sizes and configurations to simplify scaling and customisation.
Bio Kill tanks are now designed with expandable sections or compartments that can be added or removed to adjust capacity.
Mixers with variable speed controls can better handle different viscosities and mixing requirements. Mixing systems come with interchangeable blades that can suit different processing needs.
At TSA, we offer a robust piping system complying with various international standards, including cGMP, 3-A, and ASME-BPE, to accommodate changes in layout and capacity. Bio Kill Tanks with easily accessible components ease maintenance and upgrades. A modular maintenance platform adjusts to different tank heights and configurations.
Enhanced User Interfaces
Significant technological advancements have focused on improving the user experience for more effortless operation and better process control.
Touchscreen interfaces provide intuitive controls and real-time data visualisation, allowing easy navigation and quick adjustments. By integrating sensors for temperature, pressure, pH, and other parameters, you can monitor the process in real time and receive alerts. These notifications can be displayed on the UI for easy tracking and control. Graphs, charts, and visual dashboards help users quickly understand complex data trends.
Customisable views and alerts can be tailored to specific user needs. Technologies like IoT and cloud computing allow remote access and control, enabling you to monitor and manage Bio Kill tanks from anywhere.
Features like guided workflows and help menus now assist the user, reducing the learning curve and minimising operator errors. You can operate the system hands-free with voice recognition technology, especially when manual interaction is restricted or limited. You can also enhance security features by implementing secure authentication and access control to ensure only authorised personnel can make changes or access sensitive data.
Conclusion
Though these impressive advancements come with challenges, such as financial investments, the more high-tech you choose, the more you need to invest. This is a common concern for leaders in the pharmaceutical industry. However, partnering with TSA can alleviate this worry. We offer innovative solutions at competitive prices. Connect with us to learn more!
FAQ’s
You can integrate Bio Kill Tank Systems with existing infrastructure using modular designs and standardised components for seamless compatibility with existing systems. Additionally, features like IoT and cloud computing can enable remote monitoring and integration with other digital systems within the facility.
While selecting a Bio Kill Tank System provider, look for their experience, reputation, and range of offerings. Choose a provider that offers comprehensive support, including installation, training, and maintenance services. Assessing the provider’s commitment to innovation and sustainability is also essential.
Advanced Bio Kill Tank Systems are designed to meet stringent regulatory standards, such as cGMP (current Good Manufacturing Practices), FDA, and EU regulations. They include features like automated data logging, traceability, and validation protocols to ensure compliance with industry standards.
Self-healing coatings contain microcapsules filled with healing agents. When the coating is damaged, these capsules break, releasing the healing agents that fill the cracks and restore the protective layer. This technology helps extend the life of the tanks by preventing corrosion and other forms of degradation.
To assess ROI, companies should consider factors such as improved efficiency, reduced downtime, lower energy costs, enhanced compliance with regulatory standards, and potential reductions in maintenance costs. A thorough cost-benefit analysis, including long-term savings and possible risks, can provide a clearer picture of the financial benefits.