If you are questioning the value of investing in sophisticated equipment like CIP/SIP systems, here’s a blog addressing your concerns.
Cross-contamination is a significant worry for pharmaceutical companies, who go to great lengths to avoid it in order to protect the brand reputation and lives of people. CIP/SIP systems safeguard the process equipment, the production process and the final product from unwanted contaminants, helping to prevent hefty penalties and product recalls.
To learn how these systems work their magic, dive right into the blog!
What Are CIP and SIP Systems?
CIP refers to Clean-In-Place, whereas SIP refers to Sanitise-In-Place. The CIP and SIP systems efficiently clean the equipment, pipelines, and tanks without disassembling them.
Where the CIP system uses water and detergent to remove residues, dirt and microbial contaminants, SIP systems use steam to sterilize the equipment and their surfaces for their sterilization.
How Do CIP/SIP Systems Prevent Cross-Contamination?
Though CIP/SIP systems may seem to be an additional cost to incur, they help prevent cost-contamination in the following ways:
- Thorough and Consistent Cleaning
The CIP/SIP systems ensure thorough and consistent cleaning and sterilization of the process equipment. For effective cleaning, these systems perform a series of steps:
- Pre-rinse: The first step is to remove loose particles and debris from the equipment and its surfaces.
- Cleaning: A combination of detergent and water is circulated through the system to break down residues like fats, protein and other trace materials that may harbour microbes.
- Rinse: The system is then rinsed with water to remove any remaining cleaning solution.
- Sterilization: In this step, steam is usually circulated through the systems at high pressure to kill any leftover microorganisms, ensuring the equipment is free from harmful bacteria, viruses, and fungi.
This systematic and repeatable process guarantees that every part of the equipment is well-sanitized and sterilized to eliminate any potential cross-contamination sources.
2) Targeted and Specific Cleaning
The CIP/SIP systems are designed smartly to clean only the surface that comes in contact with the product. These intelligent solutions enable them to clean the targetted areas only, like transfer paths, tanks, valves and pipes, thus reducing the chance of cross-contamination.
3) Minimizing Human Error
Manual cleaning of the process equipment can introduce contaminants, leading to ineffective cleaning and potentially contaminating the systems. In contrast, The CIP/SIP systems prevent contamination by eliminating human contact, thus reducing the risk of manual errors. These automated systems consistently achieve high cleanliness standards by removing variables such as inconsistent cleaning times, improper chemical concentration, or missed spots.
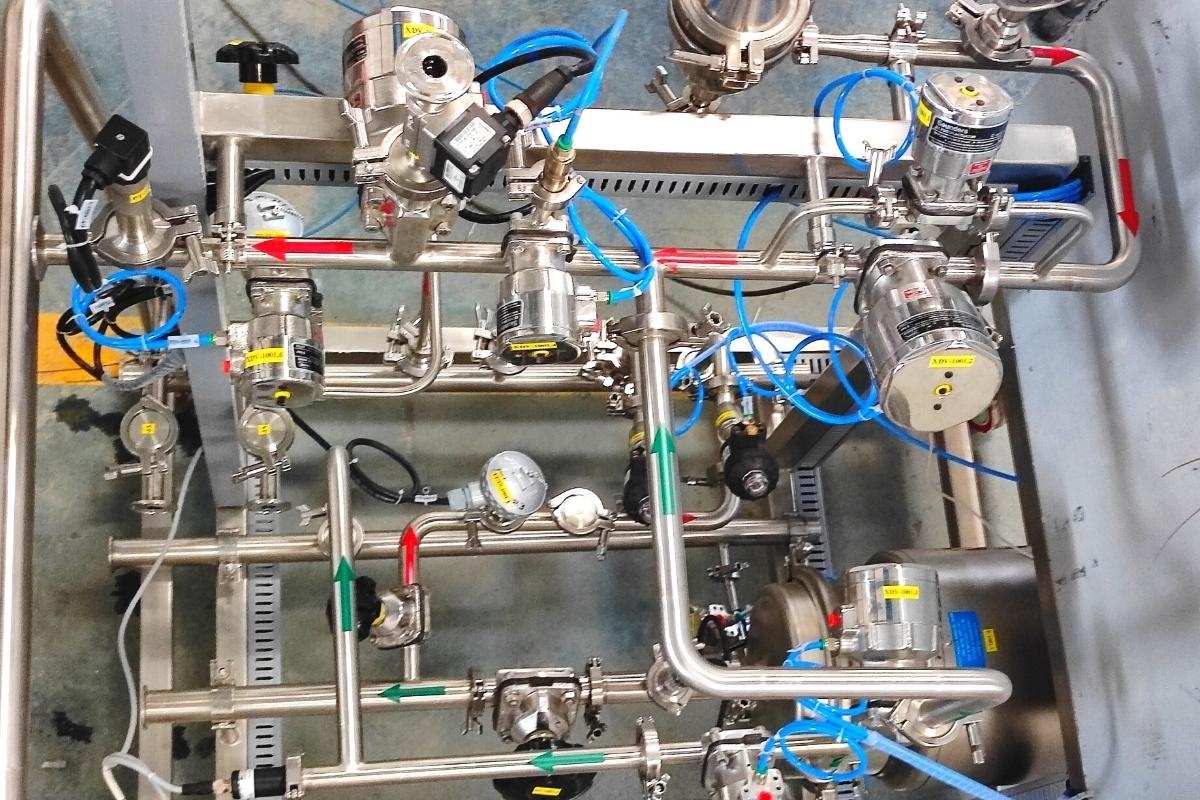
4) Closed System Design
The CIP and SIP systems operate within a closed loop, meaning the cleaning and sterilization process is carried out within sealed equipment, pipes, and vessels. A closed system design prevents contaminants from entering the system from the surrounding environment during the cleaning process while ensuring the harmful microbes within the process equipment do not escape into the atmosphere. The CIP and SIP system guarantees the safety of the personnel and the environment during the cleaning operations.
5) Practices Validated Cleaning Procedures Only
As it rightly said, “To err is to be human,” it may be challenging to monitor and keep a record of cleaning procedures implemented. In such cases, CIP and SIP systems automatically clean and sanitise the system and follow only the validated procedures. One should look for validated systems, as validation includes assessing factors such as temperature, chemical concentration, and cleaning time, ensuring that every step of the cleaning process meets regulatory standards.
TSA offers validated CIP and SIP systems designed to meet the world’s most stringent pharmacopoeia standards. Our Technology incorporates static or dynamic spray balls that work in conjunction with temperature, time duration and spray concentration to ensure a thoroughly sanitised process.
We understand that customers need customisation. Here are the options we offer:
- With or without
- tank CIP system
- Hex
- dosing system
- One/two
- tank CIP
- pump design
- Centralised CIP and local recirculation skids
- Combo CIP + SIP system
What’s more?
We provide additional support, including validation documentation, cleanroom FAT facilities, AMCs, and spare parts.
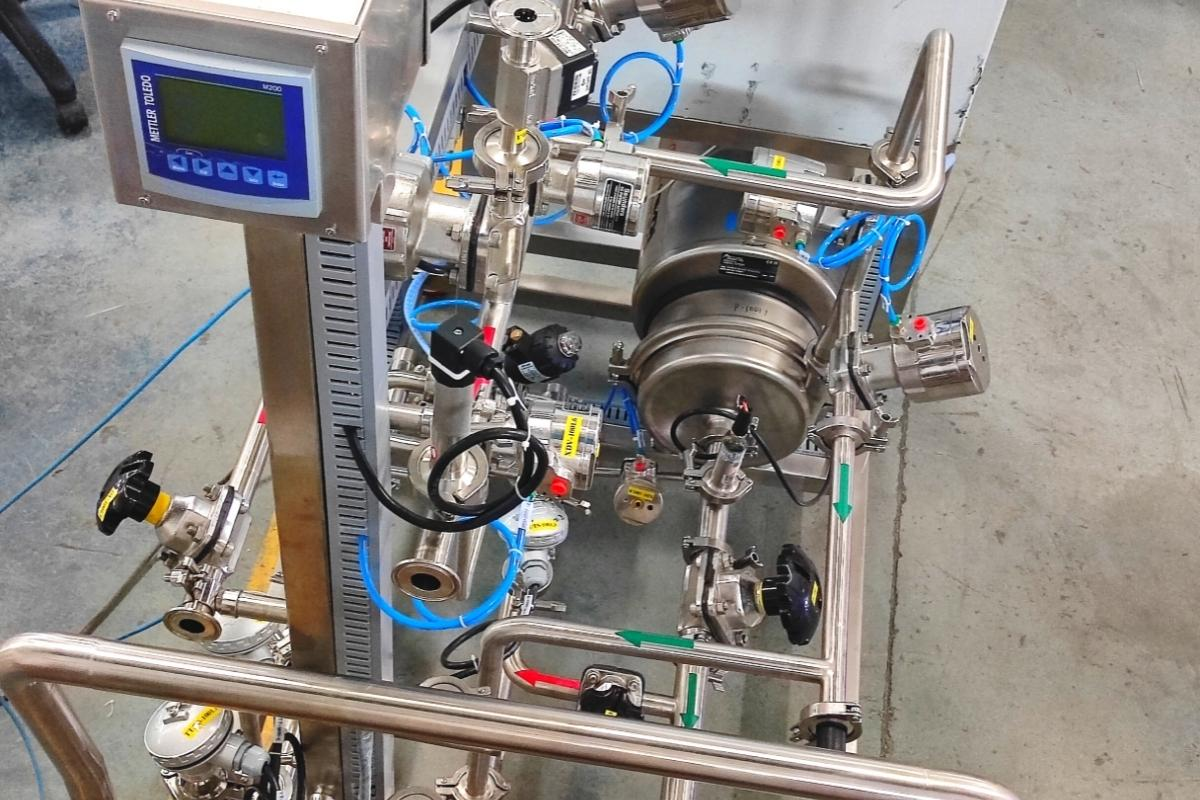
6)Cross-Contamination Risk Mitigation
For industries like Pharmaceuticals, Biotech and Biopharma, where the presence of even trace contaminants can pose serious health risks, the CIP and SIP systems offer an essential layer of protection. These systems help mitigate the risk of cross-contamination by:
- Preventing product residues from previous batches from contaminating the new products.
- Sterilizing the process equipment between the product batches to prevent any bacterial or viral transfer.
- Ensuring that different APIs and chemicals don’t mix unintentionally. This is especially important in the pharma industry, where the active ingredients must be handled precisely to avoid harmful reactions.
Advantages of using CIP/SIP Systems
- Enhanced Product Safety
Since CIP/SIP systems clean and sterilize the process equipment thoroughly, they confirm that the products are free from harmful contaminants, helping companies to provide guaranteed safer products for the consumers.
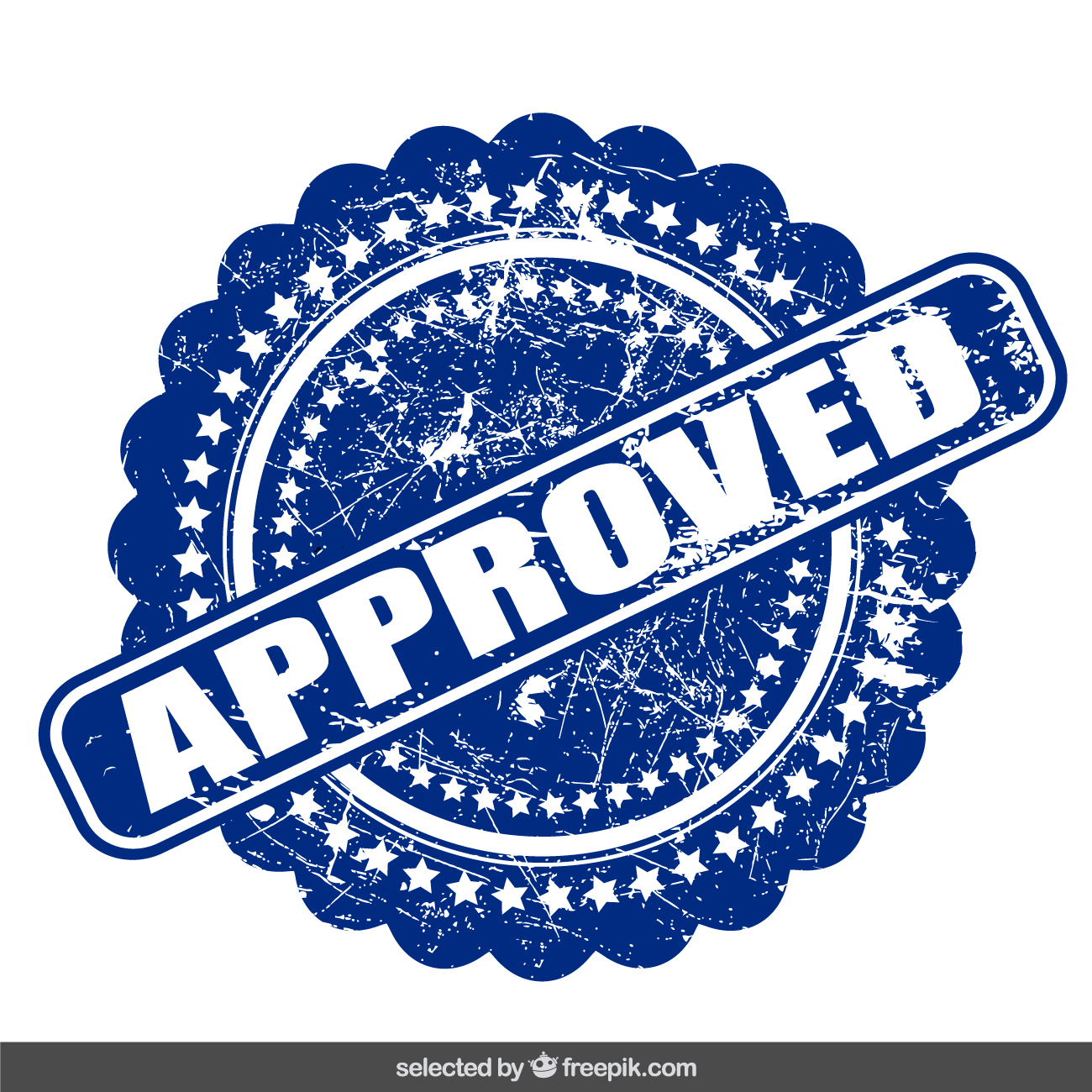
- Improved Compliance
FDA is getting strict with its regulatory standards, especially for the pharma and food processing industries. Adopting CIP and SIP systems can help companies meet the cleaning and sterilization standards set by health authorities in a better and more efficient manner.
- Reduced Downtime
Reliance on automated systems like CIP and SIP to clean process equipment saves personnel time, which can be used for making other informed decisions. These intelligent technologies also reduce downtime and increase the overall efficiency of production, as there is no requirement for disassembling and reassembling the equipment.
TSA offers CIP/SIP systems mounted on skids to simplify handling and save time. Watch the video of our Mobile CIP/SIP skid here:
Mobile CIP/SIP Skid by TSA Process Equipments
- Cost Efficiency
In addition to helping you align with your sustainable development goals, the CIP/SIP systems also help you cut costs by consuming less resources, like water and detergent. As they help prevent cross-contamination, costly product recalls and rework are also avoided.
Conclusion
As we wrap up this discussion, I hope we have effectively addressed your concerns, just as our CIP/SIP systems eliminate contaminants.
TSA offers premium quality process equipment at affordable prices. Contact us now to bring these reliable systems into your operation.
FAQs
- What safeguards exist to ensure that CIP/SIP systems don’t introduce contaminants themselves?
CIP/SIP systems are constructed from sanitary, corrosion-resistant materials (like stainless steel) that do not react with cleaning agents or the products being processed. Additionally, the systems are enclosed and sealed to prevent external contamination during operation.
- How do CIP/SIP systems reduce the risk of contamination compared to manual cleaning?
Manual cleaning relies on human intervention, which can introduce contaminants through contact, inconsistent cleaning methods, or incomplete rinsing. CIP/SIP systems eliminate most of these risks by automating the process, ensuring each cleaning cycle is uniform and highly controlled.
- Do CIP/SIP systems undergo validation for effectiveness against cross-contamination?
Yes, CIP/SIP systems are subject to validation and testing to ensure they meet industry standards for cleanliness and sterilization. Validation includes testing the cleaning agents, cycles, and temperatures to verify that all contaminants are effectively removed and that cross-contamination risks are minimized.
- How often should CIP/SIP systems be maintained to prevent cross-contamination?
Regular maintenance is essential to ensure CIP/SIP systems function effectively. Maintenance schedules vary by industry, but they typically involve checking seals, nozzles, pumps, and sensors to ensure optimal performance and prevent contamination due to equipment wear or failure.
- Are CIP/SIP systems environmentally friendly compared to manual cleaning?
CIP/SIP systems often use water, chemicals, and energy more efficiently than manual cleaning. Automated control over cleaning cycles minimizes waste and ensures that resources are used effectively, which can contribute to a more environmentally friendly cleaning process.